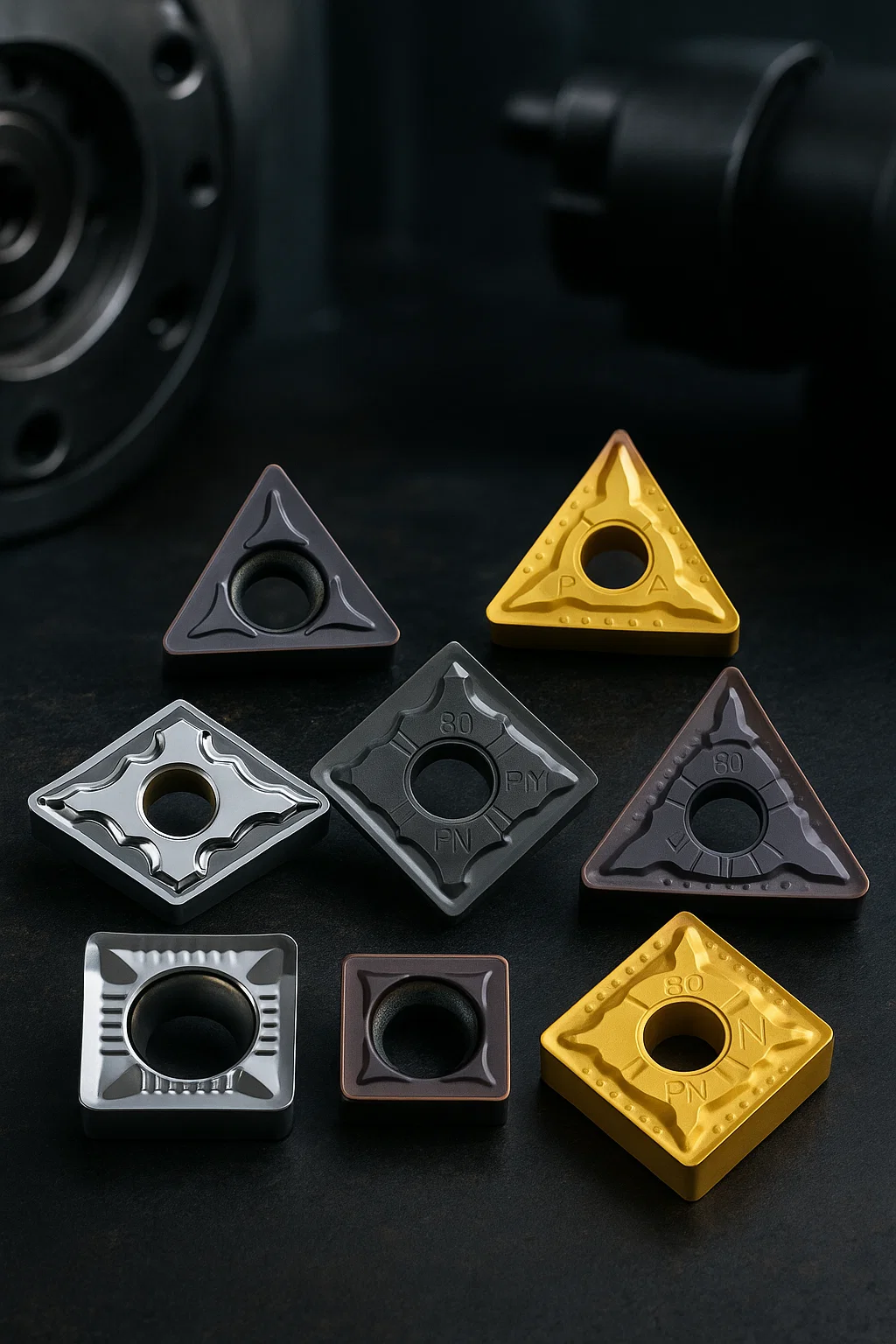
ZENCARB Carbide Inserts: The Apex of Precision & Performance in CNC Machining
ZENCARB Manufacturing Advantage: The Science of Our Inserts
- Proprietary Carbide Grades: “Our inserts feature an exclusive range of tungsten carbide grades, meticulously developed through extensive R&D. Each grade is formulated to provide optimal balance between hardness, toughness, and wear resistance, tailored for specific material groups and cutting conditions. This includes advanced binder compositions and ultra-fine grain structures for superior edge integrity.”
- Advanced Coating Technologies: “ZENCARB employs sophisticated PVD (Physical Vapor Deposition) and CVD (Chemical Vapor Deposition) coating technologies. Our multi-layered, thin-film coatings are engineered at the atomic level to enhance thermal stability, reduce friction, prevent crater wear, and significantly extend tool life in high-temperature and abrasive environments.”
- Precision Pressing & Sintering: “Our manufacturing process utilizes high-tonnage precision pressing and advanced HIP (Hot Isostatic Pressing) sintering techniques. This ensures maximum density, eliminates porosity, and guarantees the structural integrity of each insert, resulting in exceptional impact resistance and consistent performance.”
- Geometric Optimization & Chip Breaker Design: “Beyond material science, ZENCARB excels in chip breaker design and geometric optimization. Our inserts feature application-specific chip breakers that ensure optimal chip evacuation, reduce cutting forces, minimize vibration, and improve surface finish, critical for high-precision CNC operations.”
- Rigorous Quality Control & Metrology: “Adhering to stringent ISO 9001 standards, our production chain incorporates multi-stage quality control. From raw material analysis (e.g., tungsten powder purity, carbon content) to post-coating inspection using advanced metrology equipment (e.g., optical comparators, SEM for microstructure analysis), every ZENCARB insert guarantees unwavering consistency and reliability.”
ZENCARB Carbide Insert Product Portfolio: Engineered for Every Application
ZENCARB’s comprehensive range of cemented carbide inserts is meticulously designed to optimize performance across the full spectrum of modern CNC machining challenges. Our portfolio is categorized by primary application
Turning Inserts
Milling Inserts
Hole Making
Threading Inserts
Applications & Industries Served
ZENCARB’s carbide inserts are the trusted choice for precision, productivity, and profitability in critical industries worldwide, including:
- Automotive & Heavy Equipment: Powertrain components, chassis, engine blocks, large gears.
- Aerospace: Turbine blades, structural components, high-temperature alloy machining.
- Die & Mold Manufacturing: High-precision cavity and core machining for complex molds.
- Energy & Power Generation: Components for turbines, oil & gas drilling.
- Medical & Precision Instrumentation: Miniature components, surgical tools.
- General Engineering: Diverse manufacturing applications requiring high-volume and high-precision CNC machining.
Our tools excel in machining a comprehensive range of materials, including: Carbon Steel, Alloy Steel, Stainless Steel (Austenitic, Ferritic, Martensitic), Cast Iron (Gray, Nodular), Hardened Steel, Superalloys (Inconel, Hastelloy, Titanium Alloys), and Non-Ferrous Metals (Aluminum, Copper)